- News and Events
- News
- 2023.05, LOCAL COATING - Global state-of-the-art
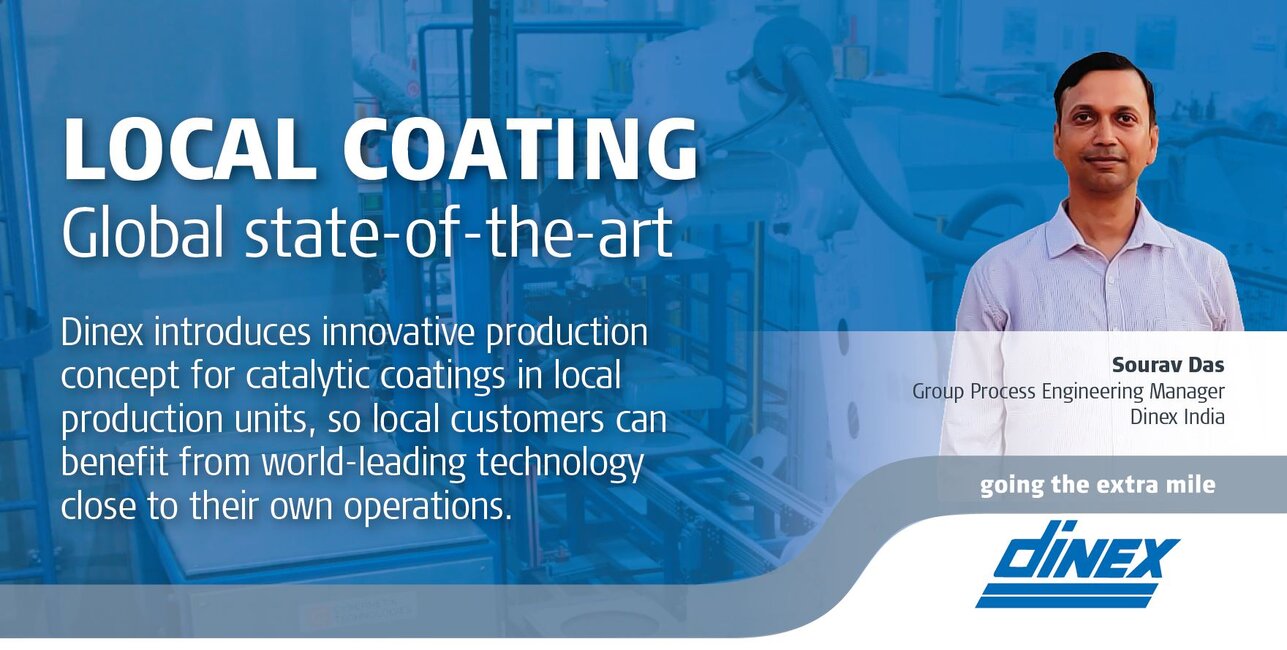
LOCAL COATING Global state-of-the-art
Dinex introduces innovative production concept for catalytic coatings in local production units, so local customers can benefit from world-leading technology close to their own operations.
Dinex has developed state of the art coating lines in China, India, and Turkey to support our local customers. These facilities also comply with local environmental norms while manufacturing is done with the latest and most competitive coating technologies.
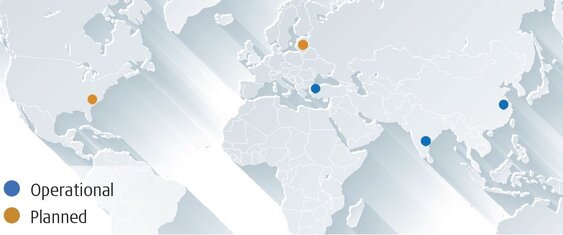
Dinex is globally present with State-of-the-Art coating production concept.
More similar coating lines are planned, as Dinex is expanding
their presence in other regions to offer all our customers the same outstanding quality and service.
Quality Built-In
These new coating lines have outstanding process control, proven with Cpk-values of over 1,67, and automation to make sure the exact amount of catalytic material is consumed while batching and coating of the formulations into products.
Dinex uses dedicated product lines where contaminations of wash-coats are not allowed as per coating technologies.
For complex products, Dinex ensures full traceability throughout all manufacturing stages and has the ability to control coating in the right orientation when it is needed for different applications of catalysts and asymmetric filter products.
Dinex coating lines uses detection and measurement systems to make sure that only substrates with the right size and right weight are processed for next operation.
The Dinex Global Coating concept supports all applicable technologies required for current and future emission regulations for Diesel, Gas and Hydrogen applications.
Applications
- Diesel Oxidation Catalyst (DOC)
- Diesel and Gas Particulate Filter (DPF/GPF)
- Selective Catalytic Reduction (SCR - Cu, Fe & Vanadium)
- Ammonia Slip Catalyst (ASC)
- Open Foil Corrugation (OFC)
- Particle Oxidation Catalyst (POC)
- SCR-coated Particulate Filters (sDPF)
- NOx Storage Catalyst (NSC)
- Zone coating for all of the above technologies
Substrates Metallic
- Cordierite
- HP-SiliconCarbide
Geometries
- Diameter: 3” – 15”
- Height 3” – 15”
Capacity
Based on standard block-concept, and may quickly be scaled up in case of additional capacity required.
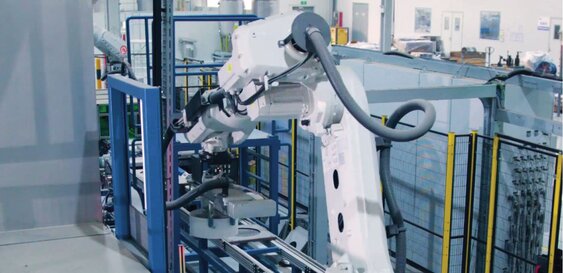
Dinex’ new coating lines are fully automated, which guarantees a high level of quality, consistency and precision throughout the entire process.
Advanced, future-proof technologies
Customers who are interested in zoned product with cost effective concepts, will also find error-proof solutions with Dinex’ coating concepts.
Dinex coating lines use robotic arms with logical programmes to ensure multiple tasks are done simultaneously in sequence. These robots are also programmed to segregate non-compliant parts based on automated inspection feedback processed at appropriate locations in production lines.
For customers with requirements to the overall system back pressure to remain within a certain range, Dinex has appropriate simulation technologies to provide solutions and coating technologies that validates the design.
Finally, Dinex coating lines have feedback control throughout the process, to ensure that the subsequent dryers and ovens are running as defined by the process setting all the time, and efficient use of energy is governed by energy management systems in all production facilities.
One global platform
To summarize, Dinex provides a single, global platform to automotive customers where emission control catalysts are manufactured with full traceability, with right raw materials and chemical compositions, precise and accurate coating on right size and orientation of substrates, with good zoned product management system, with automated robot based logical controls and segregation (if needed) and maintaining good backpressure ranges, efficient high performing activated catalyst, with energy management and environmental compliances.
By using the same, simple concept globally, but still maintaining local Process Engineering capabilities, Dinex has also made an agile solution that reduces product development and scaleup time, while still benefitting from global experiences and competences. Once again, in the true nature of our strategy: Global and Local.
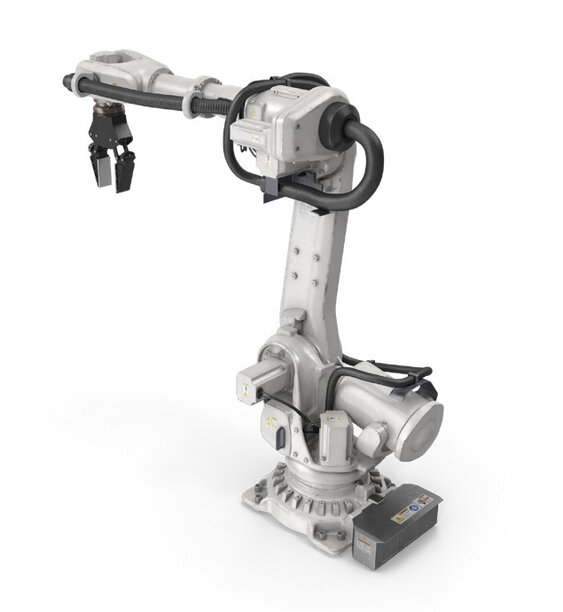
A glimpse of the Dinex OEM Division
Global Footprint - Local Presence
Operating with local teams close to our customers, backed up by global technical competences.
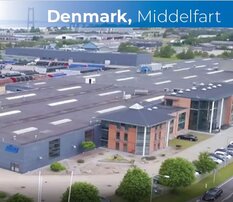
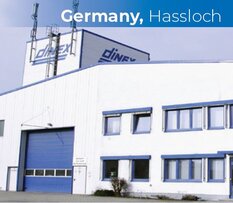
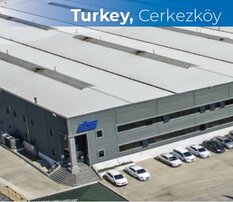

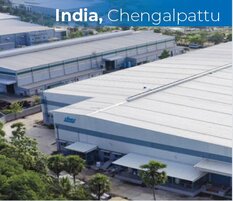
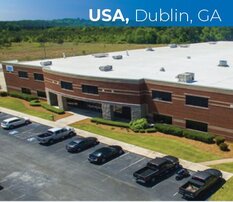
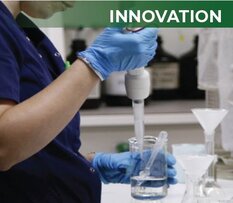
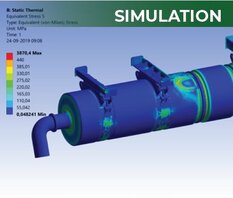
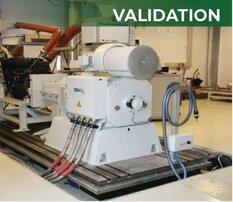
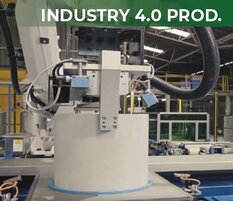
Core Technologies - Proven Solutions
All developed and produced in-house for a simple, cost efficient supply chain with highest solution ownership.
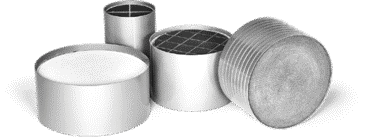
Ceramic and Metallic
Substrates with catalytic coating
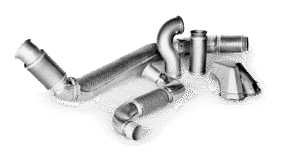
Pipes, Zero-Leakage Decoupling
and Thermal Management
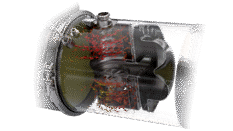
Canning and system integration
with optimal flow and mixing
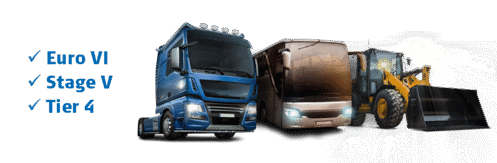
Agile Partnership - Customized Innovations
Full System and customer specific engineering approach: From final application down to coating formula.
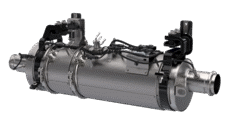
In-line system
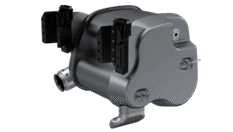
Box system
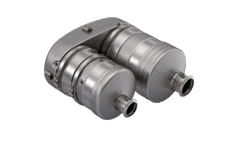
U-Shape system
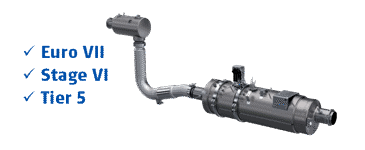
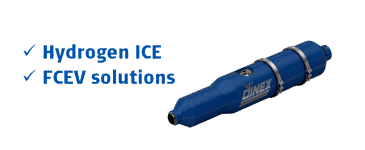